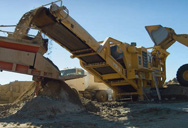
Mineralogical properties and co-sintering characteristics of fluxed ...
2023.7.25 To investigate the feasibility of co-sintering of fluxed iron ore with magnetite concentrates, the mineralogical properties of a novel fluxed iron ore were
Charlar en Línea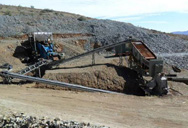
Investigation of dephosphorization of brown iron ore concentrates
2014.1.10 Brown iron ore concentrate Sinter roasting Magnetic separation Micro-X-ray spectral analysis 1. Introduction The aim of this work is to study the behavior of
Charlar en Línea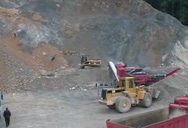
Phosphorus reduction behavior of high-phosphate iron ore during ...
2022.8.22 Thus, a method for phosphorus removal by gasification in the hydrogen-rich sintering process was proposed. In this study, the reduction mechanism of
Charlar en Línea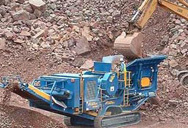
Characteristics and Sintering Mechanisms of Iron Ores
2023.4.27 Magnetic property studies demonstrated that an iron conc. contg. 88.72% magnetic iron oxides with a max. satn. magnetization of 41.393 emu/g could be produced from roasted ore which was
Charlar en Línea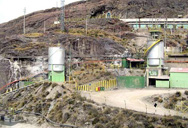
Iron Ore Sinter - an overview ScienceDirect Topics
Iron ore sinter /pellets are redirected from the wall of the blast furnace to the center using the bell-less top charging equipment. The top gas utilization (TGU) improves from 47.5 to
Charlar en Línea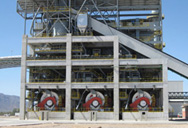
Improvement of Sinter Productivity by Control of Magnetite Ore ...
decreased and gangue component has increased in the sinter feed ore. Increase of gangue is not only the factor to influence sinter qualities, but also the factor to increase coke
Charlar en Línea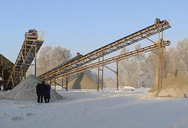
Mineral and Technological Features of
2021.3.24 Iron ores are represented by unoxidized ferruginous quartzites (magnetite, hematite–magnetite, and magnetite–hematite), as well as products of oxidation zones and ancient weathering crusts (oxidized
Charlar en Línea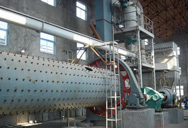
Characterisation and magnetic concentration of an iron ore
2019.1.1 In this study, we discuss the particle-size distribution, chemical composition and the mineralogy of a tailings sample of iron ore come from gravity (jigging)
Charlar en Línea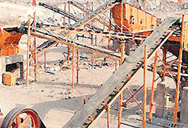
Iron Ore Sintering: Quality Indices - Taylor Francis Online
2017.5.17 Read this article. Sinter plants process a mixture of iron ore fines, recycled ironmaking products, slag-forming agents and solid fuel (coke) with the finality
Charlar en Línea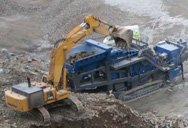
Iron Ore Processing
Key words : L ow grade iron ore, beneficiation, gravity, magnetic, sinter, pellet . 1. Introduction India is one of the leading producers and exporters of ir on ore in the world with over 28 billion tonnes of iron ore reserves [1]. P rocessing of low grade iron ore is inevitable as a r esult of increase in production and
Charlar en Línea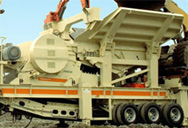
Variation in Iron Ore Sinter Mineralogy with Changes
2022.9.30 The target basicity of iron ore sinter is set by blast furnace slag composition requirements, and therefore varies with the proportion of acid burden such as lump iron ore and pellets. Increasing
Charlar en Línea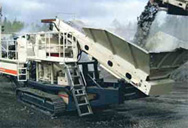
Influence of return sinter size on productivity and quality of iron ore ...
2022.1.30 The return sinter (-5 mm), which is produced inadvertently in sintering process, is recycled back and makes up to 25-30% of total sinter feed mix.
Charlar en Línea
Minerals Free Full-Text Quantitative Investigation of MgO,
2022.2.24 Secondary hematite (SH) is a serious factor resulting in reduction degradation of iron ore sinter in a blast furnace; however, until now, a quantitative study for SH formation had not been reported. In this work, the effects of gangue composition, including MgO, Al2O3 and SiO2, on the solid-state formation in the sintering process of
Charlar en Línea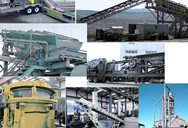
The impact of goethitic ore types across the value chain
2017.5.17 Powdery or dusty ores have goethite with an appreciable portion of goethite crystallites less than 0.01mm diameter. Goethitic ores can enhance sinter productivity. Fine ochreous goethite enhances granulation in sintering. Vitreous goethite does not granulate as well, due to smooth surfaces.
Charlar en Línea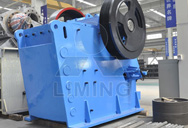
Minerals Free Full-Text Dry Permanent Magnetic Separator:
2022.9.9 Dry permanent magnetic separators have been widely used in the mineral and coal processing industries due to their simple operation and high separation efficiency. These tools not only discard some amount of bulk gangue from the raw ore, thereby reducing the volume of the grinding operation and cutting energy consumption, but also
Charlar en Línea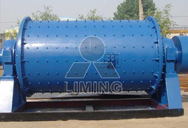
Characteristics and Sintering Mechanisms of Iron Ores with a High ...
2023.4.27 Characteristics and Sintering Mechanisms of Iron Ores with a High Proportion of High-Al 2 O 3 Limonite. April 2023; ACS Omega 8(18) ... In turn, the main materials used for a sinter are iron ore.
Charlar en Línea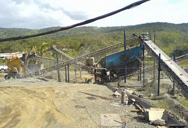
Iron Ore - 2nd Edition - Elsevier
4.2 Mineralogical characteristics of iron ore and sinter. 4.3 Automated optical image analysis. 4.4 Application of automated OIA to natural and sintered iron ore. ... 9.5 Challenges and recent advances in upgrading low-grade iron ores using magnetic separation. 9.6 Summary. References. Chapter 10 Non-magnetic physical separation of
Charlar en Línea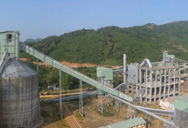
Efficient iron sintering process control - Materials Talks
2020.11.4 The feed is placed on a sintering bed, where thermal agglomeration (1300-1480 °C) takes place to produce clustered lumps, aka iron sinter (5-20 mm in size). At a common sinter plant, the following sinter quality parameters need to be controlled: Basicity, CaO/SiO2 – FeO (Fe2+) Sinter strength index, SSI. Tumbler index, TI.
Charlar en Línea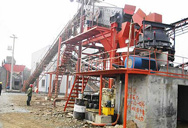
Magnetite Iron Ore Market Report Global Forecast From 2023 To
The Global Magnetite Iron Ore Market size is projected to grow from USD XX million in 2022 to USD XX million by 2030, at a CAGR of XX%. The growth of the market can be attributed to the increasing demand for steel and medication. Asia Pacific is expected to be the fastest-growing region during the forecast period.
Charlar en Línea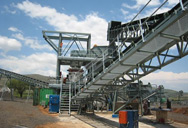
A Study on High-Grade Iron ore Beneficiation to Reduce
2020.5.21 Iron ore pellets are largely characterized by inherent physical and chemical properties of the ore. Alumina and silica play important roles in determining the productivity of a Blast Furnace. On average, one percent increase in iron content improves productivity by 2% and reduces coke consumption by 1%. Therefore higher iron ore feed
Charlar en Línea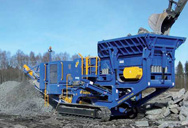
A Process Intensification Approach to Improve Productivity
2023.2.17 Various innovative initiatives undertaken to intensify the sintering process are narrated in this paper. Intensification of the iron ore sintering process is approached with a four-way framework covering granulation improvement, waste gas recycling, fuel gas injection into the sinter bed, and reduction of stack emissions.
Charlar en Línea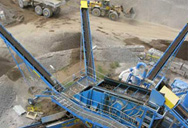
Beneficiation and agglomeration of manganese ore
2018.1.1 Sinters are as strong as Iron ore sinters and have T.I of +75 % and A.I. of less than 5 % . As Iron ore sinters pose no problems in Blast furnace charging or operation,
Charlar en Línea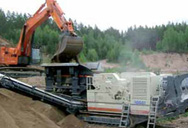
Vanadium–titanium magnetite ore blend optimization for sinter ...
2015.4.30 Zhou et al. (2015) studied that the fundamental high temperature properties of V-Ti ores and their blends and revealed that the method of V-Ti iron ore blend optimisation for sinter strength based ...
Charlar en Línea
Steelmaking Slag Beneficiation by Magnetic Separator and
sinter flux requirement in the sinter blend with also providing the recovery of significant amount of Fe and Mn from the waste [23]. With respect to chemical characteristics, slag of the 0-10 mm fraction is better than sintered ore, since it behaves as iron ore material and flux simultaneously. When BOF slag is
Charlar en Línea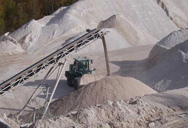
(PDF) A Review of Calcium Ferrite in Sintering of Iron Ore and The ...
2023.2.28 addition in low and high silica iron ore sinter to improve sint er to improve sinter reducibility at JSW Steel Limited[J]. Ironmaking Steelmaki ng, 2014, 41(4): 270-278.
Charlar en Línea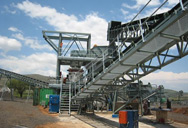
Improvement of Sinter Strength and Reducibility through
Since magnetic iron ore is generally magnetite (Fe 3O 4), we have focused on it. Generally, in case of high blending ratio of magnetite ore in sinter mixture, Fe2+ in the iron ore sinter increases, which results in lower reduc-ibility.1) Therefore, in the sintering process, promoting magnetite oxidation to hematite is important for high reduc-
Charlar en Línea
Influence of Sinter Parameters on CO Emission in Iron Ore ... - MDPI
2022.7.15 Carbon monoxide is the major hazardous component in flue gas exhausting from the iron ore sintering. This study aims to reduce the CO emission by changing the sinter parameters by sintering pot tests; specifically, the sinter quality, CO concentration, and total emission in sintering flue gas were analyzed in detail. The sinter
Charlar en Línea
Pellet, iron ore concentrste, sintered iron ore: buy from Metinvest ...
Iron ore concentrate is produced from the magnetite iron ore in the beneficiation process and is used for the production of pellets for blast furnaces and sinter. The concentrates are non-toxic, non-flammable and non-explosive. The concentrate is shipped as a bulk commodity by rail using the open-top rolling stock and by sea. Manufacturer: SevGOK.
Charlar en Línea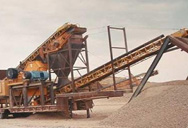
(PDF) Study on the Characterisation and Processing of Iron Ore
2018.9.1 Silin, Huben, Wotruba, and Ognyanova (2018) investigated the processing of low-grade ultra-fine iron ore after dry grinding, which resulted in improved recovery of magnetite concentrate by reverse ...
Charlar en Línea