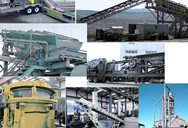
Effect of grinding media on the milling efficiency of a ball mill
2022.1.1 Abstract. The size of grinding media is the primary factor that affects the overall milling efficiency of a ball mill (e.g. power consumption and particle size breakage). This article...
Charlar en Línea
Comparison of grinding media—Cylpebs versus balls
2004.11.1 Discrepancies were found in the literature regarding grinding efficiency using Cylpebs. It was claimed by the manufacture (Doering International) that for a given
Charlar en Línea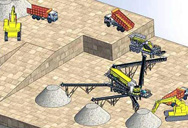
Grinding efficiency with balls or cones as media - ScienceDirect
1989.6.1 Grinding efficiency with balls or cones as media. Int. J. Miner. Process., 26: 141-151. The current study is concerned with the development of a methodology for
Charlar en Línea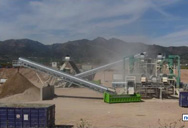
(PDF) Grinding Media in Ball Mills-A Review
2023.4.23 media decreased the grinding efficiency due to the irregular movement of the concave-convex grinding media. Concave grinding media have larger specific areas than spheres, which...
Charlar en Línea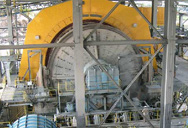
Effect of ball and feed particle size distribution on the milling ...
2018.6.1 In this article, alternative forms of optimizing the milling efficiency of a laboratory scale ball mill by varying the grinding media size distribution and the feed
Charlar en Línea
(PDF) A Comparative Study of Energy Efficiency in Tumbling Mills
2021.4.29 An evaluation of Relo grinding media (RGM, Reuleaux tetrahedron-shaped bodies) performance versus standard grinding media (balls) was made through
Charlar en Línea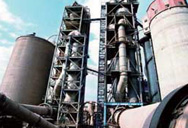
Effect of grinding media on the milling efficiency of a ball mill - Srce
of ball load composition, by varying the grinding media size distribution (e.g. alternatively by mixing four groups of 19.5, 38 mm; 19.5, 50 mm; 38, 50 mm and 19.5, 38, 50 mm), on
Charlar en Línea
An innovative approach for determining the grinding media
2021.1.22 The optimal media proportion was φ 50 mm: φ 40 mm: φ 30 mm = 28%: 28%: 44% via wet grinding experiment, in which the yield of qualified granular material
Charlar en Línea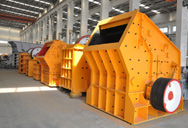
Metals Free Full-Text A Comparative Study of Energy Efficiency
Although there are no quantified statements on what range of improvement in energy efficiency has been achieved for tumbling mills when changing the shape of grinding
Charlar en Línea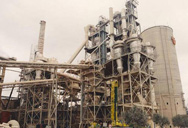
The kinetics and efficiency of batch ball grinding with cemented ...
2020.6.1 The micro-mechanism of ball grinding is considered to be a loose-bed comminution [1]. Therefore, types of balls have significant effects on the grinding
Charlar en Línea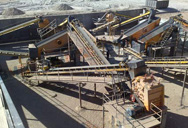
(PDF) INVESTIGATION OF EFFECTS OF GRINDING
2015.10.20 Power consumption and product size datas were considered and effects of grinding media shapes to efficiency of ball mill was explained. Discover the world's research. 25+ million members;
Charlar en Línea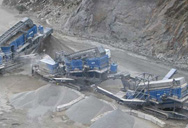
Effect of Grinding Media Size on Ferronickel Slag Ball
2021.12.27 The aim of this study is to evaluate the effect that the size of grinding media exerts on ferronickel slag milling efficiency and energy savings. A series of tests were performed in a laboratory ball mill using
Charlar en Línea
Grinding Media, Grinding Balls - NETZSCH Grinding
The grinding media, also referred to as grinding balls or grinding beads, serve as the tools in mills with freely moving grinding media, such as agitator ball mills. The movement of these grinding balls within the mill
Charlar en Línea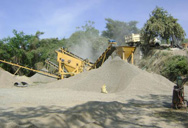
An innovative approach for determining the grinding media
2021.1.22 The dry grinding experiment was operated in the ball mill (Φ460 × 600 mm) with steel ball as grinding media at mill speed . Conclusion (1) An innovative approach for determining the grinding ball system based on grinding kinetics and linear superposition principle was proposed. The grinding experiment was operated
Charlar en Línea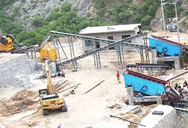
Enhance Your Milling Efficiency with High-Quality Steel Grinding Balls
2023.10.20 By selecting high-quality steel grinding balls and optimizing their usage, you can enhance your milling efficiency, improve product quality, and ultimately achieve better results in your operations. Whether you are in mining, cement production, chemicals, pharmaceuticals, or ceramics, the right choice of grinding media can make a significant
Charlar en Línea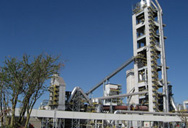
Effect of the size of media on grinding performance in stirred mills ...
2012.6.1 Based on the specific productivity and grinding efficiency, the appropriate grinding parameters were ascertained as follows: material ball ratio of 0.7, ceramic ball medium size ratio (10 mm: 15 mm: 20 mm = 3:2:5), stirring speed of 110 rpm, grinding concentration of 50%, and medium filling rate of 90%.
Charlar en Línea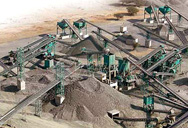
The effects of grinding media shapes on the grinding kinetics
2013.2.1 Herein, an innovative approach for determining the grinding media system of ball mill based on grinding kinetics and linear superposition principle was proposed. The optimal media ball size of −2 + 0.45 mm, −0.45 + 0.15 mm, and − 0.15 mm feeding samples were 40 mm, 30 mm, and 30 mm, respectively.
Charlar en Línea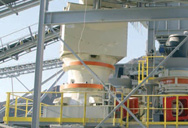
(PDF) Effect of Grinding Media Size on Ferronickel Slag Ball
2022.1.30 In this test series, three loads with the same mass of single size grinding media (balls), i.e., 40, ... The lowest grinding efficiency in terms of SSA production (2121 m 2 /kg) at the .
Charlar en Línea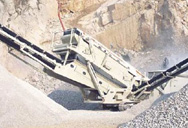
The kinetics and efficiency of batch ball grinding with cemented ...
2020.6.1 Grinding balls were selected as shown in Table 1 for these reasons: firstly, it was observed that only balls smaller than 40 mm may show significant effects of media on grinding kinetics in small laboratory mills (20 cm diameters or smaller) [10]; secondly, to mimic the charge motion in industrial mill, the ratio of mill cylinder’s diameter to maximum
Charlar en Línea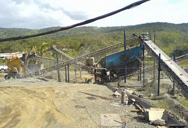
Grinding Media in Ball Mills for Mineral Processing
2023.11.23 The grinding media properties affect the overall performance of the grinding process, with grinding media size distribution being more significant than the density, shape, and hardness. Operational parameters such as grinding media filling, pH, mill speed and wear also affect ball mill efficiency.
Charlar en Línea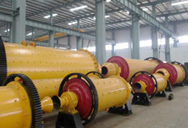
Grinding media Magotteaux
Our Grinding Media Products. We offer a full range of grinding media and grinding balls to suit our customers’ needs. Magotteaux is the only company able to provide you with a complete range of grinding media,
Charlar en Línea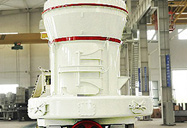
An innovative approach for determining the grinding media
2021.1.22 Semantic Scholar extracted view of "An innovative approach for determining the grinding media system of ball mill based on grinding kinetics and linear superposition principle" by Jianwen Yu et al. ... the experimental study shows that the effect of ball material ratio on the grinding efficiency Expand. 4.
Charlar en Línea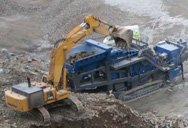
Analiza efektywności mielenia w młynach kulowym i prętowym
2022.6.5 grinding copper ore processed in O/ZWR KGHM PM S.A. The aim of the research was to evaluate the efficiency of grinding in a drum mill dependably on the grinding media used (balls, rods) for various feed parameters - i.e. particle size distribution, mix of lithological type generating different susceptibility to grinding.
Charlar en Línea
The Effect of Grinding Media on Mineral Breakage Properties
2021.12.11 The diameters of the grinding media, i.e., the steel balls, were 10 mm, 13 mm, 16 mm, 19 mm, 22 mm, 25 mm, 28 mm, and 32 mm, and the weight corresponding to the steel balls of each size was 8107.7 g, 8017 g, 8109 ... However, the grinding efficiency was low since the diameter of the steel balls was small.
Charlar en Línea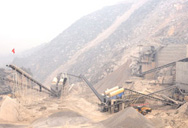
Energy-Efficient Advanced Ultrafine Grinding of Particles Using
2023.7.10 The present literature review explores the energy-efficient ultrafine grinding of particles using stirred mills. The review provides an overview of the different techniques for size reduction and the impact of energy requirements on the choice of stirred mills. It also discusses the factors, including the design, operating parameters, and feed
Charlar en Línea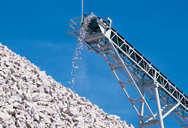
Effect of grinding media on the milling efficiency of a ball mill
173 Effect of grinding media on the milling efficiency of a ball mill Rudarsko-geološko-naftni zbornik i autori (The Mining-Geology-Petroleum Engineering Bulletin and the authors) ©, 2021, pp. 171-177, DOI: 10.17794/rgn.2022.2.14 Figure 1. Mastersizer 3000 instrument (Yanbu Cement Company Lab, KSA) Table 1: Experimental setup and conditions Mill
Charlar en Línea
How to choose proper grinding media for your ball mill
2021.2.24 Steel balls are one of the most widely used grinding media in cement ball mills, their diameters can range from 20mm to 120mm according to different grinding requirements. In a cement ball mill, generally, φ50–100mm steel balls are used in the coarse grinding chamber, φ20–50mm steel balls are used in the fine grinding chamber. 2.
Charlar en Línea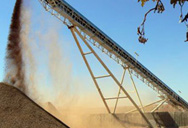
Effect of ball and feed particle size distribution on the milling ...
2018.2.1 In this article, alternative forms of optimizing the milling efficiency of a laboratory scale ball mill by varying the grinding media size distribution and the feed material particle size ...
Charlar en Línea
(PDF) A Comparative Study of Energy Efficiency in Tumbling Mills
2021.4.29 Standard Bond tests showed a reduction in the Bond ball mill work index (wi) of the mineral sample used in this study when using Relo grinding media. The modified Bond test procedure is based on ...
Charlar en Línea