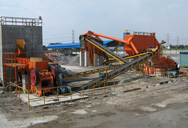
OK™ Raw and Cement Mill - FLSmidth
Our best-in-class OK™ Mill is a globally successful vertical roller mill solution for grinding raw material, cement and slag. Its cutting-edge design features consistently deliver the
Charlar en Línea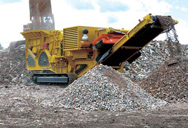
Raw Mill – Raw Mill In Cement Plant AGICO Cement Raw Mill
Cement ball mill and cement vertical mill are two raw mills commonly used in cement plants. As the main cement equipment in the cement production line, the two cement
Charlar en Línea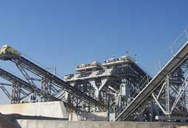
Analysis of Raw Mill Machines Maintenance in Cement
2020.5.30 In this study, the engine studied was the Raw Mill machine at plant. The raw mill machine functions as a main material grinder in
Charlar en Línea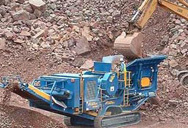
Cement Raw Mill in Cement Plant for Cement Raw Meal Grinding
Raw Mill. Feeding size: ≤30mm. Capacity: 21-210t/h. Functional advantages: Wet and dry operation, fully-functional. Applications: It widely used in cement production, silicate
Charlar en Línea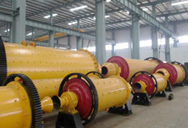
Cement mill - Wikipedia
A cement mill (or finish mill in North American usage [1]) is the equipment used to grind the hard, nodular clinker from the cement kiln into the fine grey powder that is cement. Most
Charlar en Línea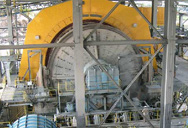
Raw Material for Cement Cement Blending Amrit Cement
90 – 95% of Limestone, 2 – 5% of Clay and 3 – 5% Laterite. The above mix proportion is ground in Raw mill at 110 – 118TPH (Ball mill) to achieve desired fineness and fed into
Charlar en Línea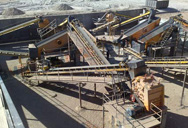
Analysis of material flow and consumption in cement
2016.1.20 The material efficiency values for a raw mill, pyro-processing tower, rotary kiln, clink cooler, and cement mill are determined to be 36.69%, 34.24%, 39.24%,
Charlar en Línea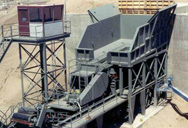
Full article: Evaluation of optimization techniques for predicting ...
The cement raw mill is the primary piece of equipment used in the modern cement industry for the raw meal production process. As a result, it is critical to investigate the exergy
Charlar en Línea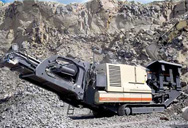
Rotary Kiln for Cement Plant - AGICO
1. Our rotary cement kilns are all made of thermal insulation material, which reduces the radiation heat loss and energy consumption during the burning process; 2. We use the compound fish scale to soft seal the front end and the back end of the rotary cement kiln. The air leakage coefficient can be thus controlled less than 10.
Charlar en Línea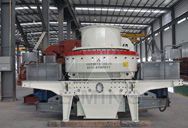
Digitization and the future of the cement plant
2020.9.16 There’s never been a more important time to build resilience into the core of the cement value chain: the cement plant. The cement industry is being hit hard by the COVID-19 pandemic, with
Charlar en Línea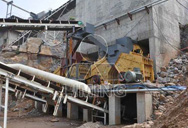
Cement Raw Mill in Cement Plant for Cement Raw Meal Grinding
Raw mill is mainly used for grinding cement raw meal in the cement factory production process. It is also suitable for metallurgical, chemical, electric power and other industrial mining enterprises to grind various ores and other grindable materials. Cement raw meal is a mixture of various raw materials before cement calcination.
Charlar en Línea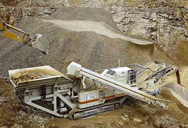
Cement Manufacturing Process and Its Environmental Impact
2023.7.10 The cement manufacturing process involves the extraction and processing of raw materials, such as limestone, clay, and shale, which are then heated in a kiln at high temperatures to form clinker ...
Charlar en Línea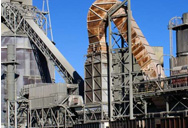
Raw Mix Preparation - ABB
Raw Mill Optimization Module The Raw Mill Optimization option controls both the temperature, the feed rate to the mill and the separator speed in order to achieve the required throughput for kiln. Where starting the mill requires dampers to be moved, to change gas flow paths, the module will also respond to these effects to keep the system
Charlar en Línea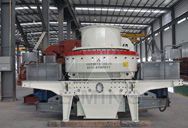
CEMENT PLANT TALK-001
CEMENT PLANT TALK-001 By: Er. Bilal Common Problems in Cement Plant One Issue from Each Section If You are facing a typical problem in your cement plant, comment us we will include that in our future issues. Quarrying: Wide variation (standard deviation) in raw material composition Crushing: Wide variation in crushed material size.
Charlar en Línea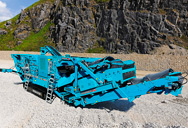
(PDF) Designing Raw Mix for Manufacturing Portland Cement
2021.10.31 The marl was used in designing a raw material mix suitable for rotary kiln feed and produced a clinker conforming to the approved specifications. The designing a raw mix consisting of 80.30% of ...
Charlar en Línea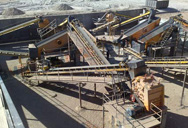
What Are the Parts of a Cement Mills? - Cement Ball Mill
2023.8.23 The production process of a cement ball mill involves raw material preparation, grinding, linearization, clinker grinding, and the eventual storage and distribution of the finished cement product. This process is integral to the production of cement, a vital building material that plays a central role in construction and infrastructure ...
Charlar en Línea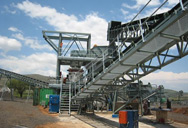
Material mix control in cement plant automation - IEEE Xplore
Abstract: The objective of this article is the development of a novel raw material mix proportion control algorithm for a cement plant raw mill, so as to maintain preset target mix proportion at the raw mill outlet. This algorithm utilizes one of the most basic and important tools of numerical linear algebra, the singular value decomposition (SVD), for calculation
Charlar en Línea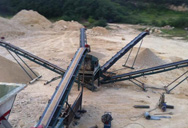
PAPER OPEN ACCESS Analysis of Raw Mill Machines Maintenance in Cement
IOP Conference Series: Materials Science and Engineering PAPER OPEN ACCESS Analysis of Raw Mill Machines Maintenance in Cement Industry To cite this article: R M Sari et al 2020 IOP Conf. Ser.: Mater.
Charlar en Línea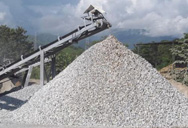
A Survey and Analysis on Electricity Consumption of Raw Material Mill
2021.1.22 In the whole process of cement production, the electricity consumption of a raw material mill accounts for about 24% of the total. Based on the statistics of the electricity consumption of the raw material mill system of 1005 production lines in China between 2014 and 2019, it is found that the average electricity consumption of the raw
Charlar en Línea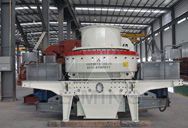
Rotary Kiln Dryer - AGICO Cement Plant
Cement dryer. Production Capacity: 1.9-76.0T/h. Specification: φ1.2×8.0m-φ 3.6x28m. Application: mineral processing, building material, metallurgy, chemical, etc. get price! The rotary kiln dryer, also called cement dryer, is one kind of rotary dryer. rotary kiln dryer apply for drying cement. The cement dryer is made of rotary body, lifting ...
Charlar en Línea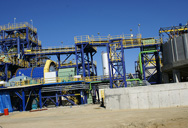
Raw Mill – Kiln Application in Cement Industry
APPLICATION CRITICALITY. The rotary kiln is the heart of a cement manufacturing plant. Cement kilns have all chemical ingredients. These. ingredients are at a broad range of gas temperatures from 100° to
Charlar en Línea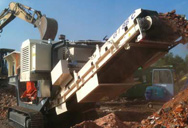
Cement Mill Cement Ball Mill Vertical Cement Mill AGICO
As a trusted cement plant manufacturer of China, AGICO Cement can provide high-quality cement mill and other kinds of cement equipment at competitive prices. Wide product range: For meeting various requirements from different clients, our cement mill range from cement ball mill, vertical cement mill, Raymond mill, coal mill in cement plant, etc.
Charlar en Línea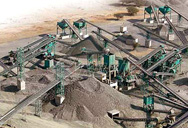
Raw Mill for Cement Plant - Fote Machinery(FTM)
Processed material: Clinker. Capacity: 50TPD. Feed size: 30mm. Discharge size: 100 mesh. Fote raw mill working site in Kenya. This raw mill is used in the material preparation of cement. The capacity is large enough to meet the requirement and the product has uniform fineness, which helped Fote get good feedback from our customer.
Charlar en Línea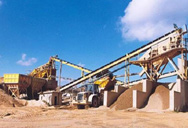
Low carbon measures for cement plant – a review - ScienceDirect
2015.9.15 Section snippets Carbon mitigation initiatives in cement plants. CO 2 mitigation measures that are discussed in this section are tabulated in Table 7.. Limitations within mitigation measures. The CO 2 mitigation measures discussed are not without their flaws and limitations. Take waste heat recovery for example, since temperatures of
Charlar en Línea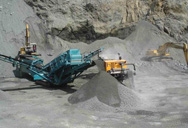
(PDF) Thermodynamic Analysis of Raw Mill in Cement Industry
2018.9.10 The simulator was used for the thermodynamic performance of a raw mill (RM) and raw materials preparation unit in a cement plant in Nigeria using actual operating data. The raw mill has a capacity ...
Charlar en Línea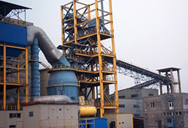
Where should online analyzer be placed for cement quality?
2018.9.24 Cement plants must monitor and analyze their raw material quality to ensure stable process operations, minimize production costs and meet product specification. Thermo Fisher Scientific. Categories. ... use of higher cost additives later in the process may be realized as well as a reduction in material variability at the raw mill.
Charlar en Línea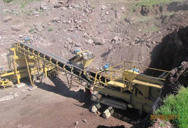
Stacker and reclaimer systems for cement plants - FLSmidth
- Mill feed system - Chemical characteristics of the materials to be handled Prehomogenisation Prehomogenisation is often necessary in the cement industry, in cases where the raw material chemical composition varies greatly. Prehomogenisation is used primarily for the main components in cement production, i.e. limestone and clay.
Charlar en Línea
Everything you need to know about clinker/cement Grinding
Previous Post Next Post Contents Everything you need to know about clinker/cement Grinding if You read and understand this article , you will be ready to be a cement grinding area manager. FEED AND FEED SYSTEM Feed Temperature Plants with satellite coolers have high clinker temperatures: e.g. Cumarebo, Oujda.. Exit satellite cooler 200
Charlar en Línea