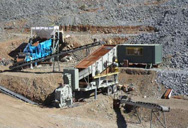
The Flotation Separation of Magnesite and Limonite
2020.3.26 The iron in magnesite ore includes the iron in the raw ore and the iron impurities entrapped in the crushing process. The iron
Charlar en Línea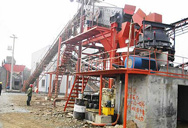
The role of sodium tripolyphosphate in wet grinding process of
2023.7.5 Sodium tripolyphosphate can improve the grinding efficiency of magnesite. • Sodium tripolyphosphate had chemical and physical adsorption on the surface of magnesite. • Sodium tripolyphosphate improved the grindability and dispersion of
Charlar en Línea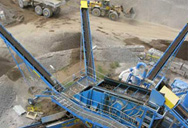
Mineral processing Metallurgy, Crushing Grinding
Whereas crushing is done mostly under dry conditions, grinding mills can be operated both dry and wet, with wet grinding being predominant. Crushing Some ores occur in nature as mixtures of discrete mineral
Charlar en Línea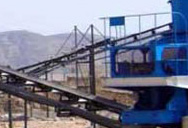
Study on regulators of purifying magnesite ore by cationic reverse ...
2021.8.20 The main useful mineral in magnesite ore is magnesite, ... Relatively pure lump ore was selected and put through a series of processes such as manual selection, crushing, screening, and grinding.
Charlar en Línea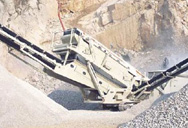
Role of surface roughness in the magnesite flotation
2022.3.1 For the ceramic ball mill, ceramic balls with diameters of 8, 12, 16, and 21 mm were utilized as grinding media. For each run, magnesite sample of 500 g was fed into the ceramic ball and ground for 4 min. A closed-circuit grinding process was adopted to
Charlar en Línea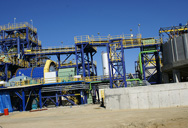
Mining and Processing Magnesite - Wiley Online Library
2006.5.31 Summary This chapter contains sections titled: Mining Operations Processing Magnesite Gravity Concentration Tertiary Crushing Postcalcination Screening and Grinding References Mining and Processing Magnesite - The Chemistry and
Charlar en Línea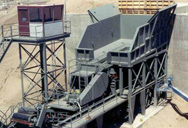
The role of sodium tripolyphosphate in wet grinding process of
2023.7.5 In this paper, in order to improve the efficiency of magnesite grinding process, sodium tripolyphosphate (STPP) was selected as a grinding aid. Grinding tests showed that STPP significantly improved the mass fraction of − 0.074 mm in grinding
Charlar en Línea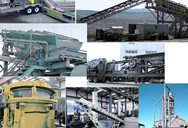
The Flotation Separation of Magnesite and Limonite Using an
crushing,sorting,grinding(XMB−Ф200×240),andscreen-ing, the single-magnesite sample was washed and dried for experimental use at a particle size of 0.021–0.075mm. Multi-element analysis of the mineral sample is shown in Table 1, and X-ray diffraction test
Charlar en Línea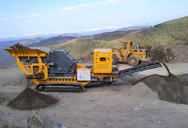
Minerals Free Full-Text Influence of Sodium Phosphate Salts
2020.11.19 The pure mineral preparation methods required for this test are manual crushing, grinding, and screening. The products under 0.106 mm fraction were collected as the microflotation test samples. The X-ray diffraction results of magnesite and
Charlar en Línea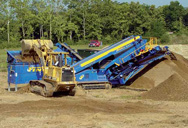
(PDF) Recovery of magnetite from dry crushed feed
2019.9.29 The Fe-oxide mineral liberation characteristics results indicated that 81.11% of the grains are full liberated, while 16.17% are the middlings and 2.72% locked in gangue.
Charlar en Línea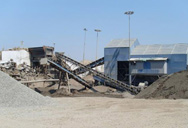
Comminution and classification technologies of iron ore
2022.1.1 Most of the high-grade hematite iron ores are typically subjected to simple dry processes of crushing and classification to meet the size specifications required for direct shipping ore (DSO). This involves multistages of crushing and screening to obtain lump (−31.5 + 6.3 mm) and fines (approximately −6.3 mm) products.
Charlar en Línea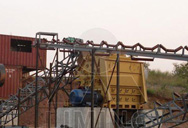
Processing of Magnesite Rich Flotation Waste Deposited on a Heap
2018.1.20 Reverse froth flotation processing was used for beneficiation of magnesite rich material – tailings from processing of primary talc ore. This possible secondary magnesite ore, which contains over 40% MgO and 45,5% loss on ignition (LOI) is stored on a heap. Because of high content of impurities it cannot be directly used. Utilizable
Charlar en Línea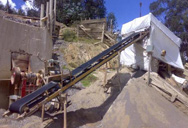
Minerals Free Full-Text A New Approach to the Grinding
2023.3.16 A new approach to batch grinding kinetics was established based on the conventional population balance model, with magnetite as the experimental object. The distribution function commonly used in the population balance model is a sum of two power functions, i.e., Bi1=φ(xi−1x1+1−φ(xi−1x1)β. Based on the new finding that the cumulative
Charlar en Línea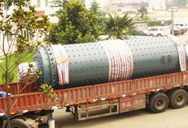
Beneficial effects of a polysaccharide-based grinding aid on
2022.4.20 Size reduction units (crushing and grinding) in cement and mineral processing plants consume up to 4% of the global electrical energy produced yearly 1.Grinding, especially in a ball mill as the ...
Charlar en Línea
A study of the grinding of magnetite/limestone mixture in a
2021.9.1 A pilot-scale grinding technology of ceramic medium stirred mill was proposed in this study. Based on the specific productivity and grinding efficiency, the appropriate grinding parameters were ascertained as follows: material ball ratio of 0.7, ceramic ball medium size ratio (10 mm: 15 mm: 20 mm = 3:2:5), stirring speed of 110
Charlar en Línea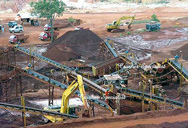
Effect of TiO2 on the Crushing Strength and Smelting Mechanism
2016.3.21 The effect of TiO2 on the crushing strength for high-Cr V-Ti magnetite pellets was studied in this paper. On one hand, the crushing strength obviously decreased with the increasing TiO2 contents. On the other hand, the crushing strength had an obvious increase after grinding treatment for the high-Cr V-Ti magnetite and titanium
Charlar en Línea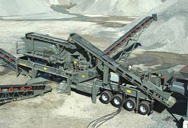
Eco-efficient and cost-effective process design for magnetite iron
2015.2.24 Option 2 has an additional grinding and magnetic separation stage compared to Option 1 and is considered to be simple for design and operation. The final milling stage is carried out using energy-efficient stirred mills. Steel grinding media usage significantly increases the operating cost. Option 3.
Charlar en Línea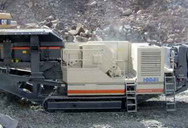
(PDF) Effect of TiO2 on the Crushing Strength and ... - ResearchGate
2016.3.21 It is found that the crushing strength has great relations with the mineral phase and microstructure. The effect of TiO2 on the smelting mechanism for high-Cr V-Ti magnetite pellets was also ...
Charlar en Línea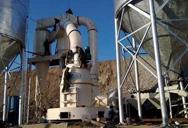
(PDF) Investigation of microcrack formation in vanadium-titanium ...
2019.10.1 Characteristics of microcracks in vanadium-titanium magnetite crushed by high pressure grinding roll (HPGR) and conventional jaw crusher (JC) were investigated.
Charlar en Línea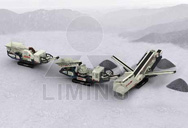
Magnesite (magnesium) Flotation Process
Whatsapp:+8615311826627. mhxu@xinhaimining. About. Mineral Processing EPC+M+O. Providing optimized solutions for your mine, one-stop service for mineral processing plant! Product. Xinhai mineral
Charlar en Línea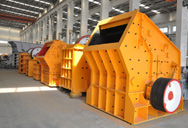
Mineral Processing SpringerLink
2017.8.24 Crushing and grinding is the most costly step in mineral processing because the power needed to liberate the minerals is very high. In this sense, grinding is commonly said to be the key to good mineral treatment and the major consumer of energy, accounting for up to 50% of a concentrator’s energy consumption ( Table 6.3 ).
Charlar en Línea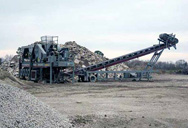
Effect of additives on grinding of magnetite ore SpringerLink
1991.8.1 Investigations have been carried out to evolve a grinding aid useful in grinding a 40% iron-bearing magnetite containing quartz as the major gangue, based on studies conducted with pure magnetite, pure quartz and its synthetic mixture.These investigations established that an addition of 200 g of CaO per metric ton of ore was the
Charlar en Línea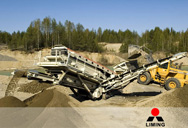
Effect of additives on grinding of magnetite ore - Semantic Scholar
1991.8.1 Investigations have been carried out to evolve a grinding aid useful in grinding a 40% iron-bearing magnetite containing quartz as the major gangue, based on studies conducted with pure magnetite, pure quartz and its synthetic mixture.These investigations established that an addition of 200 g of CaO per metric ton of ore was the
Charlar en Línea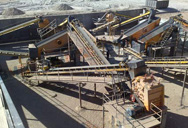
Crushing And Grinding Of Magnesite Mineral
Dunite could be used to sequester CO 2 and help mitigate global climate change via accelerated chemical rock weathering.This would involve the mining of dunite rocks in quarries followed by crushing and grinding to create fine ground rock that would react with the atmospheric carbon dioxide.The resulting products are magnesite and silica which
Charlar en Línea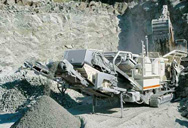
Minerals Free Full-Text Economic and Socio-Environmental Benefits ...
2020.10.26 In our previous studies, we demonstrated the performance of novel superfine crusher and pneumatic planar magnetic separator as energy-efficient technologies for dry processing of magnetite ores. The present study investigates the economic and socio-environmental benefits of applying these technologies in conceptual dry
Charlar en Línea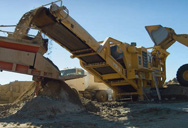
How to crush the very hard iron ore magnetite? - LinkedIn
2023.2.1 Crushing very hard iron ore magnetite requires a different approach than crushing other types of ore. The following steps can be used to crush magnetite: Pre-treatment: Before the ore is processed ...
Charlar en Línea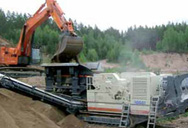
Effect of Slurry Concentration on the Ceramic Ball Grinding
2022.12.6 Ceramic grinding, which in this paper is defined as a method of using ceramic materials as grinding media, is favored by many processing plants as an emerging high-efficiency and energy-saving grinding method. This paper investigates the effect of slurry mass concentration on the grinding characteristics of magnetite by taking the feed
Charlar en Línea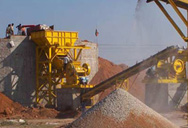
mineral crushing and grinding Mining Quarry Plant
2013.3.15 Crushing And Grinding Of Magnesite Mineral 29 Views. The kefid is the professional mining equipments manufacturer in the world, ... Mineral Crushing and Grinding Circuits: Their Simulation, Optimisation, Design, and Control by A J Lynch – Find this book online.
Charlar en Línea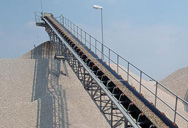
Beneficiation of Magnetite Ores - MDPI
2020.10.26 minerals Article Economic and Socio-Environmental Benefits of Dry Beneficiation of Magnetite Ores Emmanuel Baawuah 1,*, Christopher Kelsey 2, Jonas Addai-Mensah 1,3 and William Skinner 1 1 Future Industries Institute, University of South Australia, Mawson Lakes, SA 5000, Australia; [email protected] (J.A.
Charlar en Línea