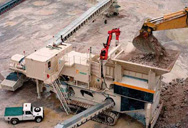
Rotary kiln process: An overview of physical mechanisms, models
2023.2.25 The main objective of their model was to analyze the physicochemical processes of clinker formation, using a heat flux function, and couple the various models
Charlar en Línea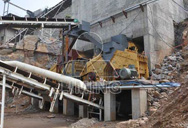
AI Kiln Solution For Optimized Control - Siemens
this solution calculates an outlook on changes in the clinker process in the rotary kiln. In this way, negative process changes can be counteracted at an early stage and the
Charlar en Línea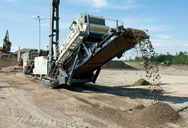
Rotary kiln process: An overview of physical mechanisms, models
2023.2.25 Heat transfer in a rotary kiln. Heat transfer plays a critical role in the preparation of clinker for a rotary kiln. Often supplied with energy by means of a burner
Charlar en Línea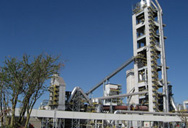
Full article: Modeling operational cement rotary kiln variables with ...
2022.10.20 In cement production, the rotary kiln is a rotating furnace tube for baking and turning the raw material into cement clinker (Sharabiany, Fatehi, and Araabi Citation
Charlar en Línea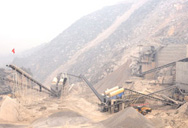
Advanced Process Control for Clinker Rotary Kiln and Grate Cooler
2023.3.3 The clinker is cooled through the action of multiple cold air fan units as it is transported within the grate cooler. The present work describes a project where
Charlar en Línea
Optimization of the Clinker Production Phase in a Cement Plant
2020.9.9 An MPC strategy is used to stabilize a temperature profile along the rotary kiln, guaranteeing good combustion conditions and maximizing production. In this paper,
Charlar en Línea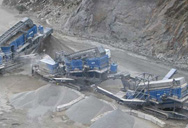
Clinker Burning Kinetics and Mechanism - Welcome to DTU
2008.3.1 Clinker formation in industrial rotary kilns is very complex due to a vast number of interacting parameters: kiln dimensions, rotation velocity, temperature, gas
Charlar en Línea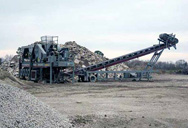
Experimental validation of multiphysics model
2022.6.19 Knowing that the clinker production via sintering in the rotary kiln constitutes most of the energy overhead in cement production, improvements in the efficiency of this process presents the greatest
Charlar en Línea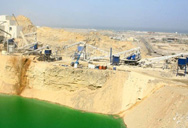
Analysis of the parameters affecting energy consumption of a
2014.5.1 Engin and Ari [10] analyzed a dry type rotary kiln system with a kiln capacity of 600 t clinker per day. They found that about 40% of the total input energy
Charlar en Línea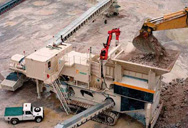
Experimental validation of multiphysics model
2022.6.19 Pyro-processing raw kiln feed of primarily calcium, silica, alumina, and iron, occurs in a rotary kiln where homogenized ingredients undergo a progressive chemical transformation in a sintering process to
Charlar en Línea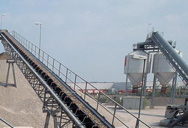
EFISIENSI CLINKER COOLER DI PT SEMEN BATURAJA (PERSERO)
2022.2.5 Semen Baturaja (Persero) Tbk. (Persero) produces cement with raw materials in the form of limestone and clay obtained from the Company's limestone and clay mining site which is located about 1.2 ...
Charlar en Línea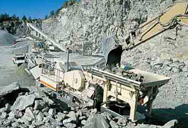
Numerical investigation of the impact of coating layers on RDF ...
2021.1.1 In a later work, Pieper et al. [13] extended their study to predict where were the regions inside the rotary kiln that exhibit coating layers from both RDF combustion and the clinker phase, i.e ...
Charlar en Línea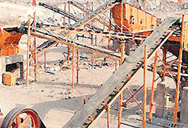
(PDF) HEAVY FUEL OIL COMBUSTION IN A CEMENT ROTARY KILN
2020.4.20 In this paper, a comprehensive 3D mathematical model for rotary cement kiln including heavy fuel oil combustion, hot flow, zone heat flux model for clinker formation and rotating wall was ...
Charlar en Línea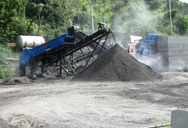
Applied Thermal Engineering - ResearchGate
Clinker production in rotary kiln system is the most energy intensive stage in cement production, accounting for about 90% of total thermal energy use [8] .
Charlar en Línea
Clinker Burning Kinetics and Mechanism - Welcome to DTU
2008.3.1 Independent of the raw meal used, the different clinker phases were formed in three stages: 1. C2S, C3A and C4AF formation at ~900-1350 °C; 2. Clinker melt formation at ~1350-1400 °C; and 3. C3S formation at >1350 °C. The first temperature of clinker melt occurrence varied slightly depending on the type of raw meal used.
Charlar en Línea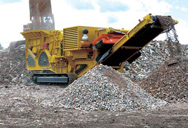
Refractory Brick Lining Measurement and Monitoring in a Rotary Kiln ...
2020.11.10 Cement clinker infiltrated into the hot faces of magnesia bricks resulting in a formation of a coat layer which protect the ... Rotary kiln is a large key rotating machine for production in ...
Charlar en Línea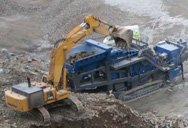
Identification and Modeling of a Rotary Kiln in Cement Plant
2021.11.25 Clinker being the essential element of cement and therefore of concrete, it qualitatively and quantitatively determines the degree of each of its properties . Consequently, the rotary clinker kiln, which is the headquarters of clinker production , represents an essential element in the improvement of these large-scale infrastructures
Charlar en Línea
Pusher Kiln NORITAKE CO.,LIMITED
Technical Support. Continuous firing furnace which conveys works on base plates using and oil pressure system. Mass production for homogeneous works and stable operation under high temperature are ensured. Maximum temperature. 1600°C. Atmosphere. Air, N 2, N 2 + H 2, H 2, O 2, Ar, CO2. Heat source. Electricity.
Charlar en Línea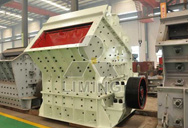
THE MOST COMPREHENSIVE ARTICLE ABOUT ROTARY KILN ON
Previous Post Next Post Contents THE MOST COMPREHENSIVE ARTICLE ABOUT ROTARY KILN ON THE WORLD WIDE WEB INTERNET It was Frederik Ransome who introduced the rotary kiln into the cement industry. For his invention, Ran some first took a patent in England (English Patent No 5442 of May 2, 1885, entiled: Improvement in
Charlar en Línea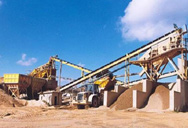
Laboratory Kiln - Made-in-China
Rotary Kiln Roller Kiln Clinker Kiln Pusher Kiln Magnetic Separation Equipment Magnetic Separator Iron Ore. More. Laboratory Dental High Temperature Programmable Small Pottery Ceramic Kiln for Gas Parts Muffle Furnace . US$ 1599 / Piece. 1 Piece (MOQ)
Charlar en Línea
AI Kiln Solution For Optimized Control - Siemens
These include increased transparency, performance improvements of the rotary kiln process, savings in fuel and emissions, and a variety of other cascading effects. With the AI Kiln Control solution helps customers to optimize their material value chain and achieve tomorrow's sustainability goals. ACKNOWLEDGMENT.
Charlar en Línea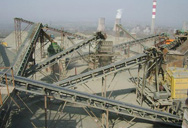
Coating and Burnability of Clinker SpringerLink
2019.8.27 Studies on the Thermal Analysis of Cement Rotary Kiln Based on Clinker Coating Materials on Refractories, Energy and Monetary Savings – Jagendran Ravindran and Soundarajan Krishnan, International Congress on Recent Development in Engineering and Technology (RDET-16) August 22–24, 2016 Kuala Lumpur (Malaysia). Google Scholar
Charlar en Línea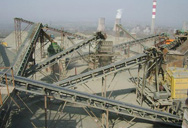
Advanced Process Control for Clinker Rotary Kiln and Grate Cooler
The cement industry includes energy-intensive processes, e.g., clinker rotary kilns and clinker grate coolers. Clinker is obtained through chemical and physical reactions in a rotary kiln from raw meal; these reactions also involve combustion processes. The grate cooler is located downstream of the clinker rotary kiln with the purpose of suitably
Charlar en Línea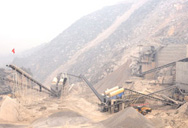
Optimization of the Clinker Production Phase in a Cement Plant
2020.9.9 The application on cement rotary kiln control is discussed in detail as a simulation example. In , a first principles model of a cement kiln is used to control and optimize the burning of clinker. An MPC strategy is used to stabilize a temperature profile along the rotary kiln, guaranteeing good combustion conditions and maximizing production.
Charlar en Línea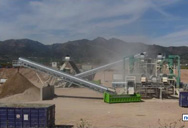
Rotary Kiln - KHD Humboldt Wedag
Just as a heart must never stop beating, so a rotary kiln must never stop turning. Which is why our kilns – whether the two-pier Pyrorapid® or a classic three-pier kiln – are engineered to keep rotating, even in the most challenging of process conditions. So, you can relax with the guarantee of reliable, trouble-free operation, 24 hours a day, seven days a week.
Charlar en Línea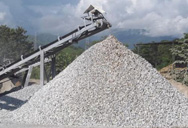
Portland Cement Clinker - an overview ScienceDirect Topics
Portland cement clinker is nodules (diameters, 5–25 mm) of sintered material produced by heating a homogeneous mixture of raw materials in a kiln to a sintering temperature of approximately 1450 °C for modern cements.The resulting clinker consists of four main minerals: 11 1. Alite or tricalcium silicate, Ca 3 SiO 5 (in oxide terms 3CaO.SiO 2),
Charlar en Línea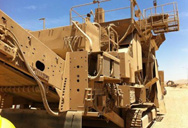
Analysis of the parameters affecting energy consumption of a rotary ...
2014.5.1 Clinker production in rotary kiln system is the most energy intensive stage in cement production, accounting for about 90% of total thermal energy use [8]. In the present study, Gaziantep cement plant located in the South-east of Turkey is considered as a case study for the thermal energy analysis.
Charlar en Línea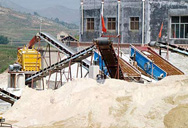
(PDF) Numerical study of a rotary kiln. Case of an industrial plant
2016.11.7 This paper summarizes the results obtained from the modeling and simulation of an industrial rotary kiln used for clinker production in order to optimize its operation and reduce fuel consumption ...
Charlar en Línea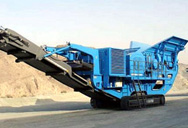
HEAVY FUEL OIL COMBUSTION IN A CEMENT ROTARY KILN:
A rotary kiln with an internal diameter of 2.3 m and a length of 55 m at Figuil Cement plant is used for this study (Fig. 1). The burner tip is at 1.5 m from the front door.
Charlar en Línea