
(PDF) Iron Ore Sintering: Quality Indices - ResearchGate
2017.5.2 Sinter plants process a mixture of iron ore fines, recycled ironmaking products, slag-forming agents and solid fuel (coke) with the
Charlar en Línea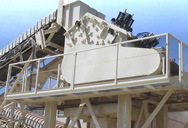
Quality requirements of iron ore for iron production - ScienceDirect
2015.1.1 Quality requirements of iron ore for alternative ironmaking processes. The BF ironmaking process relies heavily on metallurgical coke and involves coking and
Charlar en Línea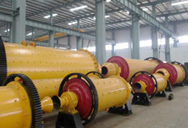
(PDF) Iron Ore Sintering: Process - ResearchGate
2017.2.16 Sintering is a thermal agglomeration process that is applied to a mixture of iron ore fines, recycled ironmaking products,
Charlar en Línea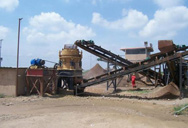
Iron ore sintering - ScienceDirect
2015.1.1 Sintering is the most economic and widely used agglomeration process to prepare iron ore fines for blast furnace use. In this chapter, the sintering process is first
Charlar en Línea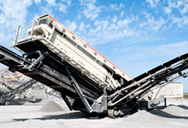
Effect of ore types on high temperature sintering characteristics of ...
2023.6.1 So sintering behaviour of adhering fines and nucleus particles differs when using lower quality iron ores and magnetite concentrate. Hence understanding of these
Charlar en Línea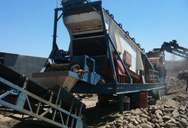
Iron ore sintering - ScienceDirect
2022.1.1 Like other sintering processes, iron ore sintering converts iron ore fines of often −8 mm in size into larger agglomerates, namely sinter, between 5 and 50 mm in
Charlar en Línea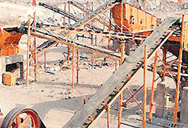
Iron Ore Sintering: Quality Indices - Taylor Francis Online
2017.5.17 Read this article. Sinter plants process a mixture of iron ore fines, recycled ironmaking products, slag-forming agents and solid fuel (coke) with the finality
Charlar en Línea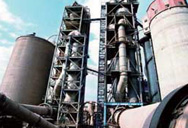
Iron Ore Sintering: Process - Taylor Francis Online
2017.3.24 Sintering is a thermal agglomeration process that is applied to a mixture of iron ore fines, recycled ironmaking products, fluxes, slag-forming agents, and solid fuel (coke). The purpose of the sintering
Charlar en Línea
Iron Ore Sintering: Quality Indices - ResearchGate
Iron Ore Sintering: Quality Indices D. Fernández-González, I. Ruiz-Bustinza, ... Sinter plants process a mixture of iron ore fines, recycled ironmaking products, slag-forming
Charlar en Línea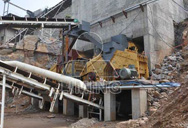
Alternative to deal with high level of fine materials in iron ore ...
2019.9.1 Nowadays, as the demand for iron ore increases together with the depletion of high grade ore deposits, mining companies have been investing to produce
Charlar en Línea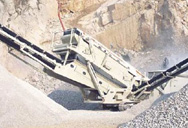
Ore Sintering - an overview ScienceDirect Topics
2010.4.2 The “ore group” iron ore textural classification scheme (Table 2.7 and Figures 2.7 and 2.8) has been developed to link ore texture to downstream processing performance including lump/fines ratio, beneficiation, blast furnace lump physical and metallurgical properties, or fine ore sintering quality (Clout, 2002).
Charlar en Línea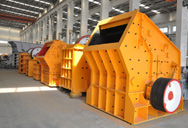
Sintering: Most Efficient Technologies for Greenhouse Emissions ...
2019.7.19 Regarding acid gas components, following values are strictly required: HF ... Fernández-González D, Ruiz-Bustinza I, Mochón J, González-Gasca C, Verdeja LF (2017c) Iron ore sintering: quality indices. Miner ... Development of an energy efficient curtain flame ignition system for sintering of iron ore fines. Int J Energy Technol ...
Charlar en Línea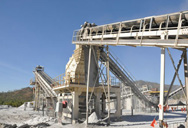
Minerals Special Issue : Mineralogy of Iron Ore
2019.5.20 Special Issue Information. Dear Colleagues, Iron ore sintering is an important stage in the production of steel from iron ore. Sinter can constitute more than 60% of ferrous burden in modern blast
Charlar en Línea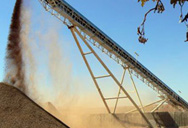
Influence of Iron Ore Sinter Base Mix Fines (− 0.150 mm) Size on ...
2021.10.16 The product ion of high strength iron ore sinter for blast furnace iron making unit was developed by optimizing the granulometry of less than − 0.150 mm fines in sinter base mix which consists of iron ore fines (− 10 mm size with 0.150 mm: 41%), beneficiation plant jig concentrate, i.e., washed ore (− 3 + 0.150 mm size with − 0.150
Charlar en Línea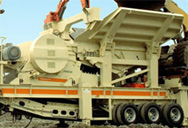
Iron ore sintering - ResearchGate
2022.1.1 Abstract. Sintering is the most economic and widely used agglomeration process to prepare iron ore fines for blast furnace use. In this chapter, the sintering process is first described to ...
Charlar en Línea
Iron Ore ScienceDirect
Abstract. Iron ore is regarded as the second most important commodity behind oil. As an essential input for the production of crude steel, iron ore feeds the world’s largest trillion-dollar-a-year metal market and is the backbone of global infrastructure. To meet the growing demand for steel products, world iron ore production has increased ...
Charlar en Línea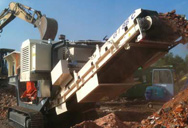
Advances in Sintering and Pellet Technology
2023.5.31 Amongst various processes used in agglomeration, sintering and pelletization are widely used in the iron ore industries. About 70% of the blast furnace feed is reporting from the sintering processes. The objective of iron ore agglomeration is to generate a suitable product of granules in terms of thermal, mechanical, physical, and
Charlar en Línea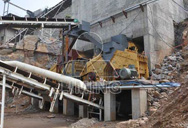
EFFECT OF MgO AND BASICITY ON MICROSTRUCTURE AND
These iron ore fines are therefore required to be agglomerated into larger pieces [1, 2]. Sintering is one of the most economic and widely used agglomeration process for preparing iron ore fines for blast furnace use. Many reactions may take place during the sintering process. Macroscopically iron sinter has a non-uniform structure
Charlar en Línea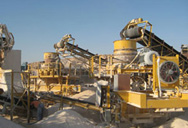
(PDF) Iron ore sintering with charcoal - ResearchGate
2012.10.14 Iron ore sintering is the main process of fines agglomeration for ironmaking with relevant particulate matter and trace element emissions of integrated steel plants.
Charlar en Línea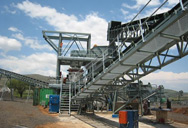
In Situ Temperature Measurement Across the Sinter Bed
2022.12.3 Sinter is one of the important inputs to Blast Furnace. Iron ore sintering process is dominating the agglomeration process in Steel manufacturing sector. To achieve good quality sinter, it is required to know the change in temperature with time for a particular segment of sinter bed. As sintering takes place in moving grate sinter machine
Charlar en Línea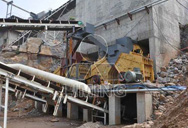
Sintering SpringerLink
2020.8.19 Abstract. The sintering process can be defined as a thermal agglomeration process that is applied to a mixture of iron ore fines, recycled ironmaking products, fluxes, slag-forming agents, and solid fuel (coke) with the objective of obtaining a product with the suitable characteristics (thermal, mechanical, physical, and chemical) to
Charlar en Línea
Innovative Development on Agglomeration of Iron Ore Fines and Iron
In steel industry and in mines, a significant amount of ultra-fines waste iron oxides and iron ore fines is generated. Utilizations of these fines are required to reduce the environmental hazards and conserve the natural resources. Some of these fines are normally used in sintering practice. However, sintering has a
Charlar en Línea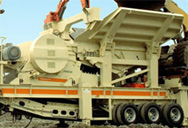
Preparation of Iron Ore Micro-pellets and Their Effect on
2018.6.13 In hybrid pellet sintering process, iron ore concentrate of relatively finer size is first converted into micro-pellets and these micro-pellets are used in place of iron ore fines. The prerequisite for micro-pellets to be used in hybrid sintering is to have sufficient green strength so that they does not get disintegrated during mixing with other raw
Charlar en Línea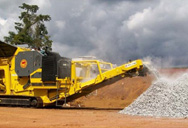
Variation in Iron Ore Sinter Mineralogy with Changes in Basicity
2022.9.30 The target basicity of iron ore sinter is set by blast furnace slag composition requirements, and therefore varies with the proportion of acid burden such as lump iron ore and pellets. Increasing the lump proportion of the burden will increase the target sinter basicity. The mineralogy of sinter produced with a range of basicity between
Charlar en Línea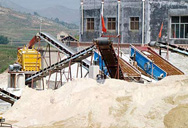
Iron Ore Sintering: Raw Materials and Granulation
2016.10.28 Abstract and Figures. Sintering is an agglomeration process that fuses iron ore fines, fluxes, recycled products, slag-forming elements and coke. The purpose of sintering is to obtain a product ...
Charlar en Línea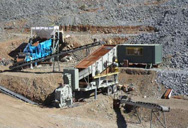
Determination method of high-temperature characteristics of iron-ore
2019.1.30 The high-temperature characteristics of iron ores play important roles in optimizing ore proportion of sintering, which are tested by using iron-ore fines and analytical reagent CaO as raw materials. Two calculation methods of CaO addition amount based on binary basicity (basicity method) and n(Fe2O3)/n(CaO) (mole ratio method),
Charlar en Línea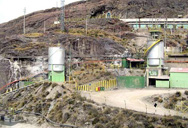
Utilization of Pellet Fines in the Iron Ore Sintering Process
2023.7.26 2.2.1 Preparation of Green Mix. An iron ore blend was prepared by mixing the iron ore fines with the required proportion of pellet fines. A small pile was prepared by layering the iron ore blend, coke breeze, flux and return fines on a weight basis, according to the proportions mentioned in Table 1.After proper mixing, these raw materials were
Charlar en Línea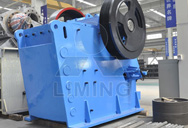
Usage of High-LOI Iron Ore Fines in Pellet Making
2019.6.8 High-LOI iron ore fines are required for detailed laboratory pelletization studies and are used in pellet making. The received iron ore is martite–goethitic and hematite–goethitic form of ore with high LOI content. The iron ore consists of 57.7% Fe, 6.19% SiO2, 2.69% Al2O3, 8.80% moisture and 8.85% LOI.
Charlar en Línea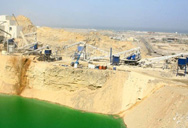
Iron Ore Agglomeration Technologies IntechOpen
2017.5.18 Sintering is a thermal process (1300–1400°C) by which a mixture of iron ore, return fines, recycled products of the iron and steel industry (mill scale, blast furnace dusts, etc.), slag-forming elements, fluxes and coke are agglomerated in a sinter plant with the purpose of manufacturing a sintered product of a suitable chemical composition,
Charlar en Línea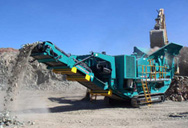
A Novel Sintering Process for Porous Iron Ore Sintering with
2022.2.28 The present work proposes a novel process to sinter porous iron ore (porosity ~23–24%) with enhanced productivity and quality. The iron ore is pre-processed in the presence of calcined lime for the temporary closure of pores, which further prevents water absorption during the granulation process in drum in the presence of water. The
Charlar en Línea